In a small rural town, a farmer struggled to maintain his old tractor, which had seen better days. He couldn’t afford to replace it, but he knew that without it, he would lose his livelihood. One day, a stranger came to the farm, offering to fix the tractor with his trusty welding equipment. The farmer was skeptical, but he had no other choice. The stranger went to work, and in a matter of hours, the tractor was as good as new. The farmer was amazed at the quality of the work and asked the stranger how he did it. The stranger smiled and revealed that he was a retired welder who had spent his life perfecting his craft.
Welding plays an important role in many manufacturing and construction industries. While there is a wide range of welding equipment to choose from, it can be difficult to make the right selection for your needs. This guide provides an overview of different types of welding equipment, key considerations when choosing welding tools, as well as safety tips for using welders. Understanding the basics behind welding equipment will help individuals confidently tackle their project and get the desired results.
Overview of Different Types of Welding Equipment
Welding is an essential skill used in many different industries and applications, so it is no surprise that welding equipment comes in a variety of shapes and forms. Some of the most common types of welding equipment include electric arc welders, MIG and TIG welders, stick welders, oxy-fuel systems, and plasma cutters. Electric arc welders use two rods to deliver an electric current needed to melt the metals being joined together; MIG and TIG welders are more accurate versions that allow you to control more variables like the size of the weld; stick welders use a single-piece electrode that melts into the metals being joined together; oxy-fuel systems involve burning combustible gas with oxygen for increased temperatures; and plasma cutters use a stream of high-velocity ionized gas (plasma) to microwave through many different materials. Each type of welding equipment has its own unique set of advantages and disadvantages depending on your specific application requirements.

Important Considerations When Choosing Welding Equipment
When it comes to welding equipment, there is a lot to consider before buying. The type of metal you are working with will determine what kind of power requirements are needed and the right size of the electrode to weld. The torch and other associated tools should be user-friendly, and lightweight, offer a comfortable grip and provide stability. Safety features such as anti-flashback are also important, given that welding can be hazardous if done improperly or with inadequate protective equipment. Be sure also to consider ratings for the amperage capabilities of your welding machine, as these will affect the quality of the welds produced. Ultimately, selecting the right welding supplies is an important part of achieving successful results in any welding project.
How to Select the Right Type of Welder for Your Needs
Choosing the right welder for your needs can be a difficult task. Before selecting a welder, it is important to assess your goals and resources first. What type of materials will you be welding? How often will you use the welder? Consider these questions before committing to any particular model. You must also consider the budget and space to store or move the unit since some welders are more expensive than others. Once you have an idea of what type of machine is best for your purpose, research different models available and compare features such as electrode size, duty cycle, and cooling system. Alternatively, consult with a professional who can identify which type of welder best suits your needs and provide safety tips to ensure safe and efficient operation while using the equipment. With careful consideration in choosing well-suited welders for your project, you will make the most out of your investment in every way.
Tips on Safely Using a Welder
Using a welder is an exciting and rewarding way to create something new, but it’s a tool that needs to be used with caution. First, be sure to wear the proper protective gear; this includes a welding helmet with filter shade 14 or higher, long pants and sleeves made from natural fiber materials (not synthetic fabric), and heavy leather work shoes. Additionally, it’s important to make sure you have plenty of ventilation for your workspace so that fumes created by the welding do not build up; this can also be achieved by using a respirator or air filter mask. Finally, never leave hot metals in the area after you’re done welding – allow them time to cool down and put them away so they won’t melt or damage any other items. With proper precautions taken and safety always top of mind, there’s nothing stopping anyone from creating beautiful projects through welding!
The Benefits of Using Quality Welding Equipment
The use of quality welding equipment is essential for a safe and successful welding job. Quality welding equipment provides superior safety and performance as well as offers greater precision and control. Quality welding equipment also offers better protection against heat, sparks, or other hazards, resulting in fewer injuries or economic losses from accidents. Using high-quality welding equipment can lead to more reliable and long-lasting welds, and can also reduce time wasted due to malfunctions or incorrect results. Furthermore, high-end welding equipment can provide much more in terms of complexity and accuracy than lower-grade tools, further increasing production speed and reducing labor costs. In short, the use of quality welding equipment can save time, money, and lives – making it an invaluable asset for any professional welder.
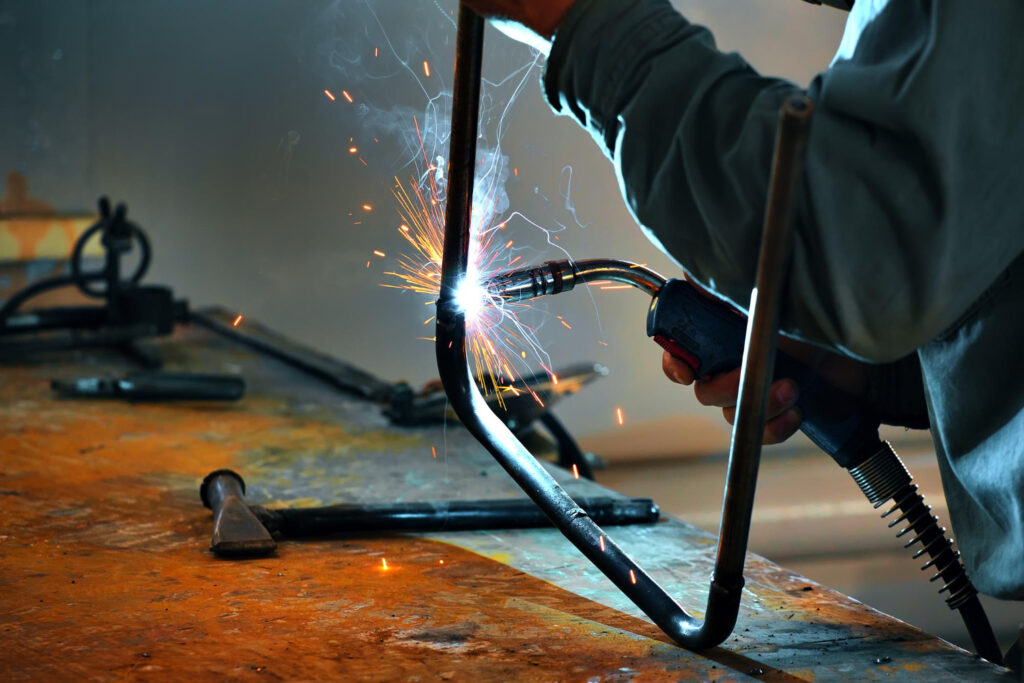
Troubleshooting Common Issues with Welders
Welders are an incredible tool for metalworking, but if the machine is not running smoothly, it can cause some frustration. Thankfully, there are quite a few common issues with welders that can be identified and resolved quickly. The first step to troubleshooting any problem is to determine its source – did the welder malfunction or is something else interfering? Next, inspect the connections and wires for corrosion or loose connections; clean or replace any damaged parts as needed. Then check for potential electrical problems like overheating leads or loose connections. Finally, if all else fails, consult with a welding expert who can help get your machine back in top condition quickly and efficiently!
Welding is an important part of many fields, and the type of welding equipment you choose can make all the difference. It’s important to know what considerations are important when choosing a welder, as well as how to select the right type and safely use it. Quality welding equipment is key to successful welds, with increased safety and efficiency relative to cheaper alternatives. In addition, should any issues arise with welding equipment, there are simple steps to troubleshoot and get back on track as quickly as possible. As a result, knowing the basics of welding equipment will help users confidently move forward in their projects and take on more ambitious endeavors.
FAQ
Welding is a process that uses extreme heat and pressure to join two pieces of metal together. During welding, the metals are melted and then allowed to cool, forming a strong and permanent bond. This technique ensures that the two pieces of metal remain connected in a durable manner.
Welding encompasses a variety of techniques, each with its own set of benefits and drawbacks. Options like arc welding, gas welding, resistance welding, laser welding, electron beam welding, friction welding and ultrasonic welding are all available for different types of metal joining applications.
Welding machines, helmets, gloves, electrodes or wires, torches, gas cylinders, clamps and safety equipment are some of the most frequent welding supplies. The type of machine used depends on the welding process chosen – for example MIG, TIG or Stick welding.